Before ordering that new metal gate, fence or railing we’ll show you how to choose the right finish in 3 easy steps plus give you 5 key takeaways to follow when getting it painted or powder coated.
There are lots of variables when considering finishes & applications on metal surfaces. Beyond styling, you should consider location, sun exposure, qualities of the metal substrate as well as the nature or performance of the powder itself.
If you’re a project manager, homeowner, designer, or contractor we want you to conquer that gate! Follow these steps the next time you’re planning a new fabricated metal project that needs painting.
Step 1: Choose the right color
As far as color matching samples, you may be surprised to learn that it’s best to start with powder color selections first. Why? Generally, there is less selection in powder colors vs liquid coatings. So if you’re trying to match something you found at Home Depot, Lowes, Benjamin Moore, Devoe, Sherwin Williams, or Valspar(Ace Hardware) you may find an exact match hard to find. A visual match, or close match, is generally the case more than not.
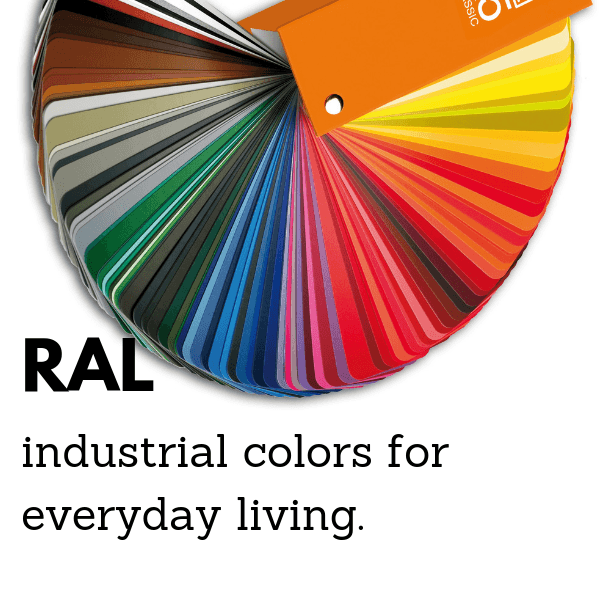
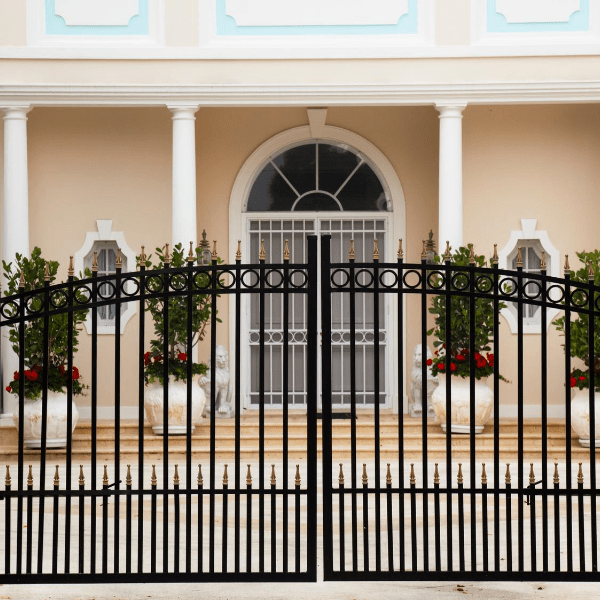
Powder by the Pound
Powders are ordered by the pound. For ease in ordering colors are sold in 5, 10, or 50+ pound boxes to the industry. A few even sell per pound. Powder coaters will generally carry a line of in-stock colors like blacks, whites, silvers, bronzes and may have powder colors left over from other jobs to choose from. If your job is smaller in scale you may opt for the in-house inventory rather than the possible added cost of special ordering a color.
For more on specific types and kinds of powder used in powder coating click here>>
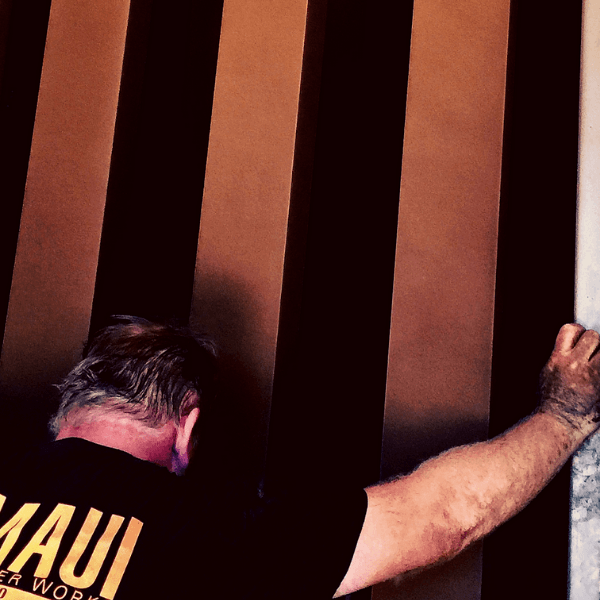
Bespoke vs Line Coaters
Custom job costs vary depending on size and complexity. For example, a straight rail fence or gate would require less powder to coat than an and ornate one because of all the angles. Flat-panel doors and gates need even more because of the amount of material it takes to cover the surface evenly.
Manufacturer Direct
If you are ordering directly from a pre-made gate manufacturer that powder coats its finishes then more than likely they are using a line system. These systems generate low-cost automation processes to stay competitive. The pieces are daisy-chained and then run through a series of corridors to complete the process.
Even though automated, it’s still important to check with them on the exact application they are doing to ensure the most protection is given to the finish. Quality and process may vary.
Step 2: Choose the right finish
It is well known that powders perform better due to the application process which makes them more UV, chemical, and scratch-resistant. They also have low VOCs(solvent-free) which is better on humans and the environment. But that’s not all. Some powders can have ratings on them.
Knowing a little more about these ratings can help you determine what to look for especially when referring to Step 1-choosing color.
Powders, Processes & Ratings
Although not certified, Maui Powder Works can apply most AAMA 2604 specified and ASA colors currently available in the finish coating industry. Mid-level coatings like 2604 rated colors are ideal for fences, railings & gates because of durability against daily use like scratching and abrasion.
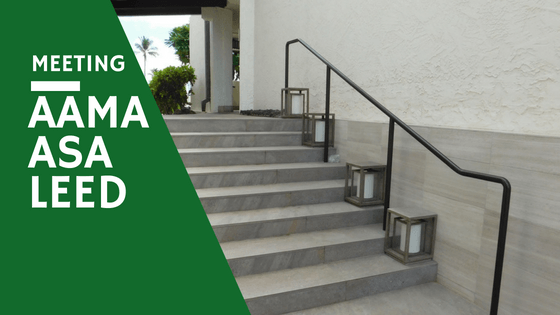
A Day In The Sun
The powders themselves have good color retention from sunlight exposure lasting at least 5yrs. Powder compliant to meet industry standards is mostly made of polyester or resin-based(TGIC) polymers.
Most super durable powders, like RALS or TG Series 38 with TigerShield, have an S Florida rating of 3000hrs. This is industry talk for the time it takes for fading to start to occur. That doesn’t sound like much but that’s good!
Read more about AAMA 2604 standards to see if this is right for you.
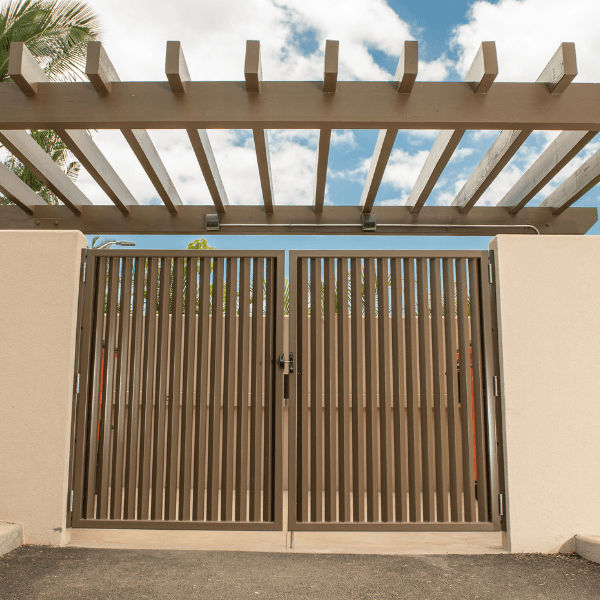
Kynar vs Powder Coating
There are even higher-rated powders and paints as in AAMA 2605 and 2606. Applicators with this certification can achieve this rating because the pre-treatment process is what guarantees the rating. A 2606 rating paint like Kynar, a PVDF based coating(plastic-based) coating offers extreme environmental exposure lasting 20+ years. These paints are set through spraying but can be cured in a conventional baked process, just like powders in powder coating. They are heavier in thickness in application. This thickness in composition aids in weathering resistance.
The Cost of Longevity
One is the cost of longevity. As in, how long do you need this project to last? For example, if we’re talking metal roofing or building exteriors then I would say, yes, you would need it to last the longest because how often will you be replacing the item over time. Probably 30-50 years?
But if your metal project is a railing or front gate then you may be changing design and style every 10-15 years then you may want to choose powder coating instead. In this case choice of colors and style win out. Powder coating becomes the best for durability and accessibility.
Susceptibility
Secondly, no chemical resistance. Just like Superman has superhuman powers, except for when exposed to Kryptonite, PVDF coatings(thermoplastics)are susceptible to solvents like M.E.K and even body oils. If the surface is going to be touched daily on things like latches, handles, and railings powder coating would be your better choice. Some powders even have anti-microbial qualities as well as wear resistance from most surface cleaners including acetone.
Side note: If you find a 2605 rated color you like you can still use it but it would only be considered similar to a 2604 application because certain steps in the prep process are not conducted to meet the rating.
A list of powder suppliers can be found on our company links page. >>>
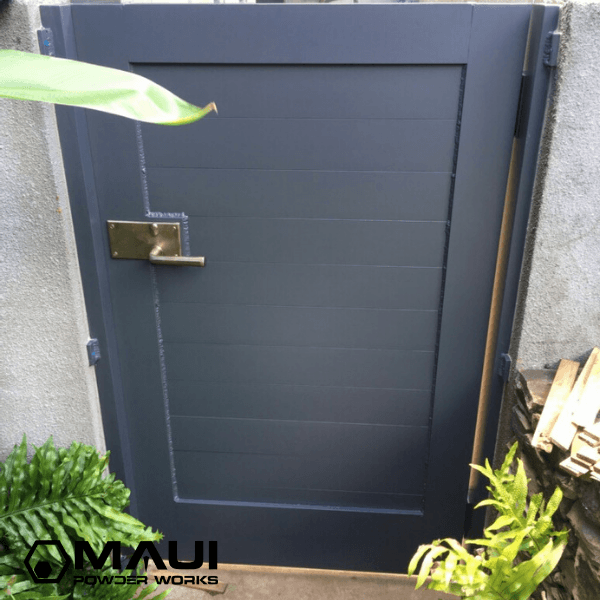
Step 3: Choose the right metal
If your design or pattern can be attained in any metal substrate then location should be your next highest priority. Outlying electrolysis from where the metal will be mounted or attached as well as using dissimilar metals can cause early decay and corrosion from the inside out. Consider your location to salt & water environments as well. Being close to the ocean or any water source, like excessive rain or lakes should be taken into account.
Use of Primers
Primers can add additional costs to finish coating but the use of them far outweighs in terms of durability & longevity. Each substrate uses a different formulation; so for steel, the primer consists of zinc, a rust inhibitor and aluminum primers have epoxy water barrier qualities.
The downside is that in exceptional places like Hawaii or Florida it is susceptible to even faster erosion than because of the extreme climate conditions there(salt & UV).
See more on that here. >>>
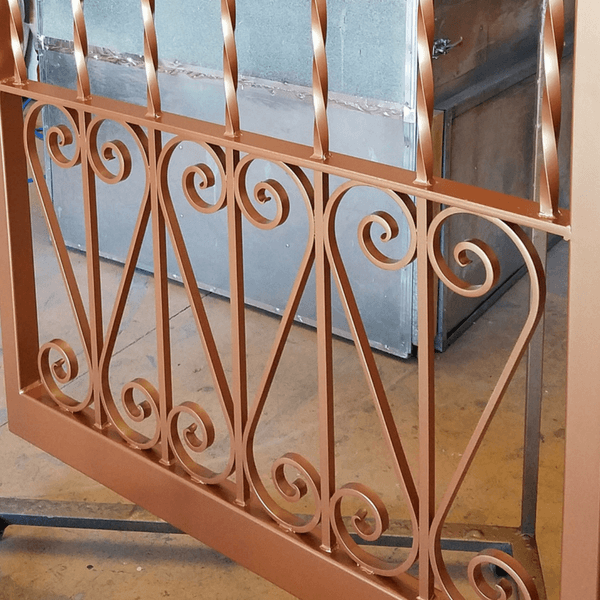
Steel & Iron
Steel and other ferrous metals generally need more prep work like sandblasting before coating because it is prone to surface rust. All metals sweat but steel is more susceptible. The only way to inhibit the rust is to include the proper pre-treatment with some kind of rust inhibitor. Although easier to work within the fabrication process than aluminum these metals are heavier. They are also much cheaper than aluminum, copper, or brass.
Aluminum & Alloys
Aluminum is an overall more expensive material but holds up better against surface decay especially near the ocean. The appeal to using this metal in new fabrications is you can go right to painting or powder coating which eliminates the cost of sandblasting steel.
The downside to using aluminum is that because of its lightweight composition, it could easily be dented. Because of it’s softer metal quality it conducts electricity easily. And that’s not good. Aluminum doesn’t rust but it will corrode. It appears as a scaly powdery white(like Alka-seltzer)on the surface. To offset electrolysis, the use of sacrificial metals are advised. Be sure to consult a welder about this.
Other Considerations
Galvanized Steel
Because steel is susceptible to rust, galvanizing Is a pre-treatment process given to steel to prevent corrosion from occurring on the surface. Although there are varying grades of galvanized steel, most will appear bumpy after it is “dipped”. Most utilitarian, military or industrial buildings like hospitalizes, prisons, ships, and schools demand these types of coatings for obvious reasons. The typical interior home railing or residence gate does not require a need for such an extreme coating. It is best to consult your architect or contractor.
Warranties
Most coaters will offer a standard 1yr warranty however if the powder coating process is done correctly you can expect longevity well beyond the minimum. We’ve done many jobs here in the islands that are 5-7yrs or older and they still look great, such as oceanfront aluminum railings. You can expect at least a minimum of 3yrs to 10-20yrs if the variables are right and you plan on maintaining it. Copies of our warranty are available upon request.
View customer testimonials here.>>>
5 Key Takeaways:
- Although color selection in powders is in the thousands, there has not been enough expansion to cover every brand of color available in the paint market.
- No matter how exotic the paint or powder, if the pretreatment isn’t good, the coating will be poor.
- Consider all components to new projects including, substrate types and use of dissimilar metals that expose you to early decay from electrolysis.
- Location is important. Where your project ends up i.e. the quality of the environment should be discussed as well as its expected longevity. This will help your coater determine the best approach and cost of the project.
- For everyday fabrications, we recommend an AAMA 2604 finish which in simple terms is a primer coat specific to the metal with an outdoor-rated color coat that provides greater durability.
About us
RossKote is committed to sharing their experience in metal coatings, painting, and restoration so customers & powder coaters can navigate the process of powder coating and make the best choices for getting their projects done.
RossKote regularly contributes helpful videos on his blog and YouTube channel.
Join us. As we build a powder coating community online to share our passion for performance finishes by subscribing to RossKote's Powder Coater Podcast
Connect with us. Comment below. What would you like to know more about? I love to answer everyday questions to the consumer market wants to know about powder coating.
MAUIPOWDERWORKS.COM
Copyright 2016-2022©